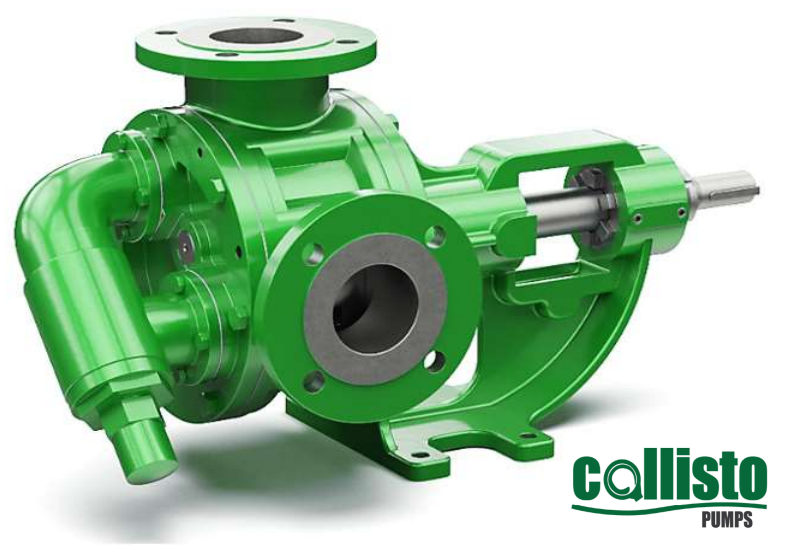
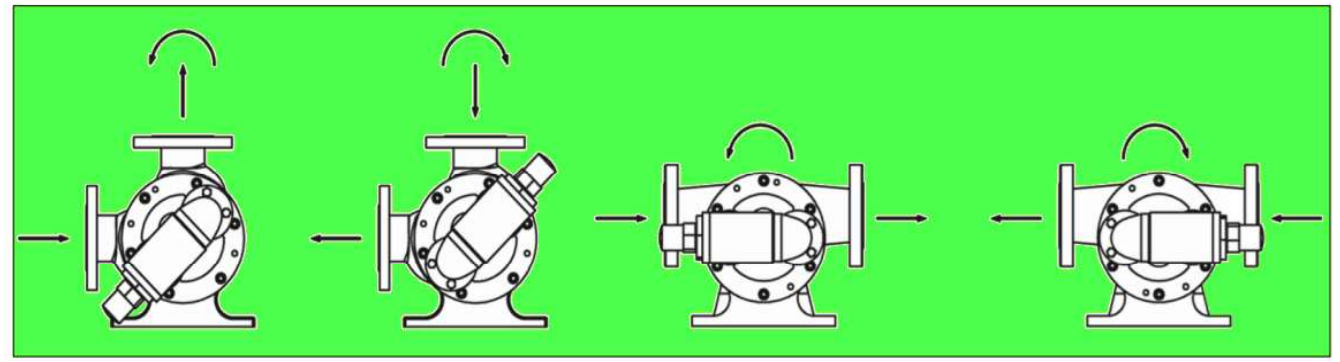
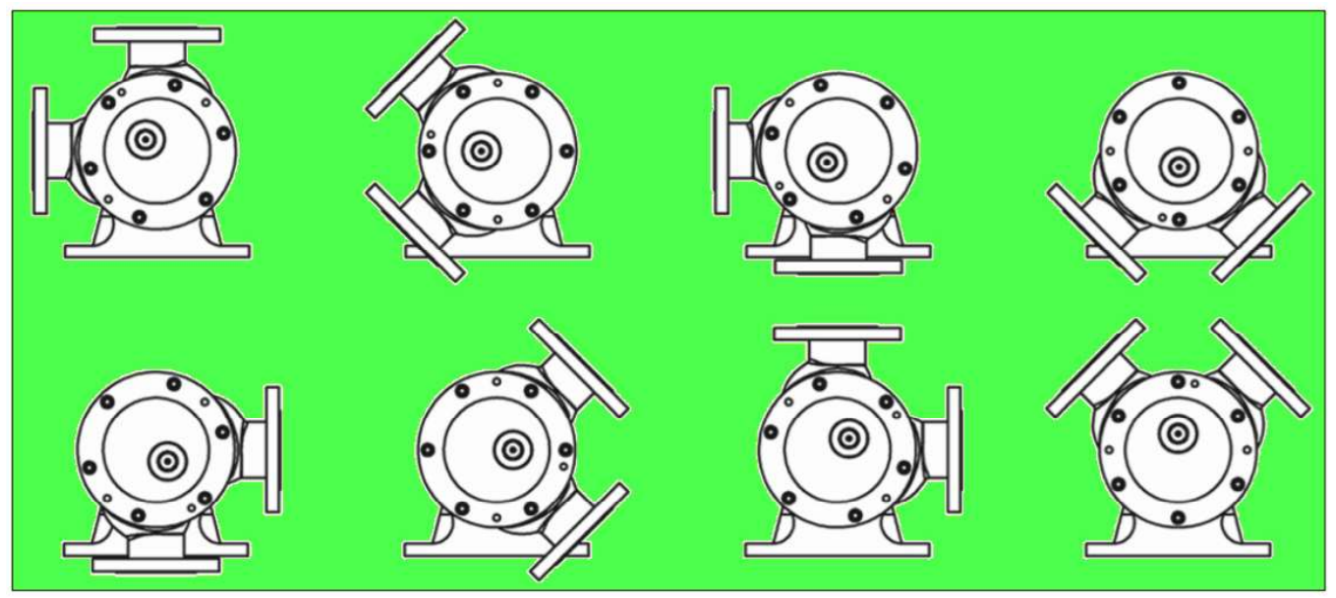
Internal Eccentric Gear Pumps
Connection sizes
: 3/8” – 8”
Capacity range
: 0.1 – 250 m3/hr
: 1 – 15 Bar
Pump body & cover
Sealing
Internal gear pump direction of rotation:
*Supplied in both clockwise and Anti clockwise direction of rotation. * Based on the direction of relief valve the orientation of suction valve can be determined. * The end cap of the pressure relief valve must always point to the suction port. * Direction of rotation can be changed by switching the direction of pressure relief valve and wiring the motor to turn in opposite.
Internal gear pump flange position:
Pump casings can be turned through 8 different orientations to enable easy installation into numerous different pipework systems. Make sure that the pressure relief valve is pointing to the suction though!
Download Catalogue
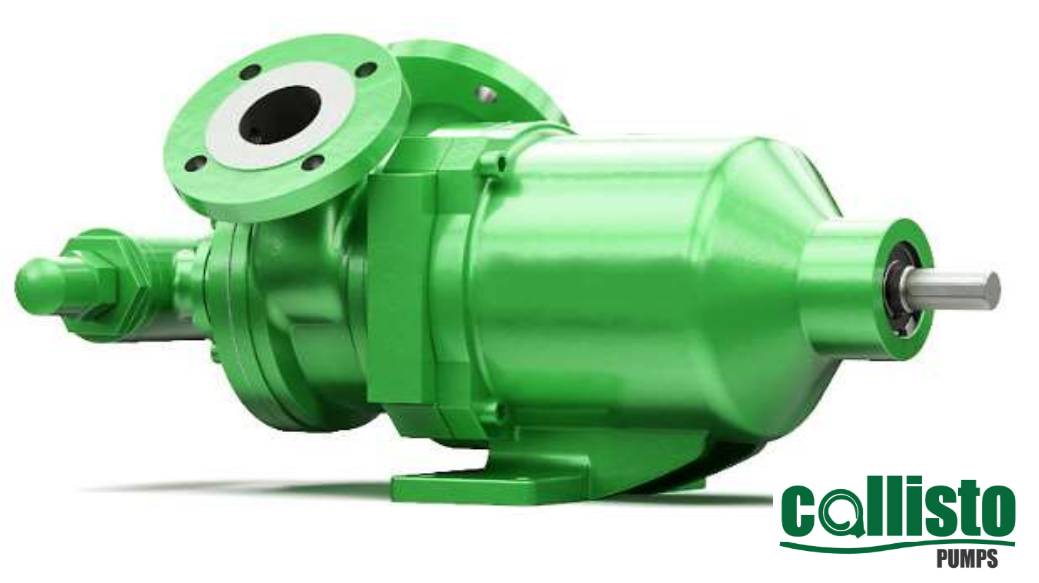
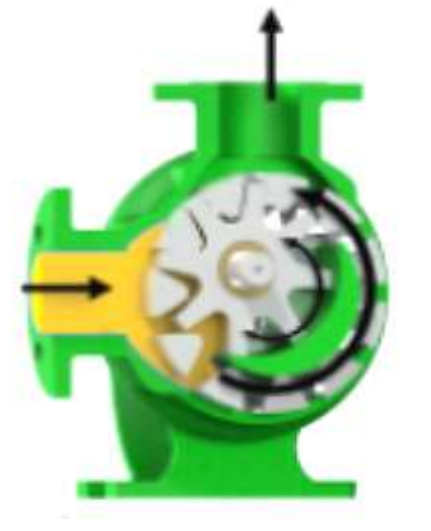
Magnetic Drive Internal Gear pumps
Connection sizes
Capacity range
Pump body & cover
Sealing
Sealless magnetic drive
Advantages of magnetic drive seal-less pump:
-
There is no any seals, Hence zero leakage
- Since there is no any seals, the pump needs little maintenance
-
Since there is no leak, the is extremely low risk of fluid and vapor emissions. Hence used to pump hazardous, flammable, explosive and toxic chemicals
-
Self priming in nature
Internal gear pump working principle:
-
Internal eccentric gear pump have only 2 moving components within the process medium.
-
Positive displacement is achieved by filling the cavity between the rotary & idler gears.
-
Fluid enters through the suction port, filling the cavity between the teeth of the gears.
-
The crescent within the pump head then separates the fluid as the idler gear turns on the pump shaft.
-
These four images demonstrate this operation in detail.
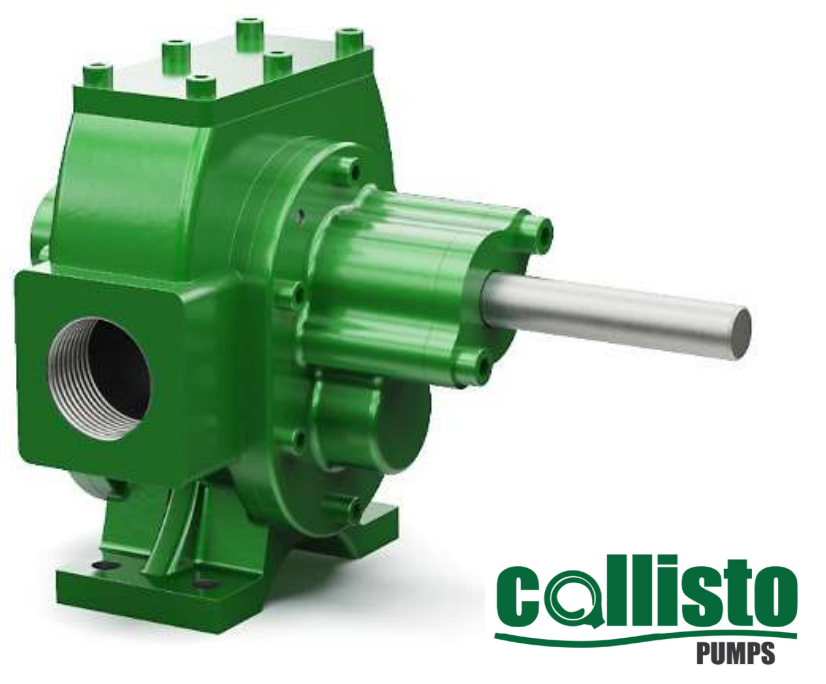
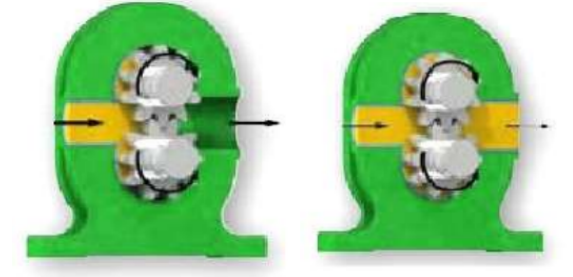
External Gear Pumps
Connection sizes
Capacity range
Pump body & cover
Cast iron / Spheroidal cast iron/ Cast steel/ Stainless steel AISI 304/ Stainless steel SS316
Sealing
Lip seal / Mechanical seal
External gear pump operating principle:
-
Similar in operation to the internal gear pump
-
The positive displacement is achieved by the fluid filling the cavities between the gears.
-
The fluid is then carried around the periphery or external areas of the gears until the casing is full filled.
-
And the fluid is pushed out of the pump outlet under pressure
Difference between external and internal gear pump:
* INTERNAL: Bulky / Easy to clean and reassemble / Smaller outlet size / All gear designs are spur / suited for shear sensitive fluids * EXTERNAL: Compact / Larger outlet size / Gear design include spur & Helical / Higher speed / Suitable for high pressure
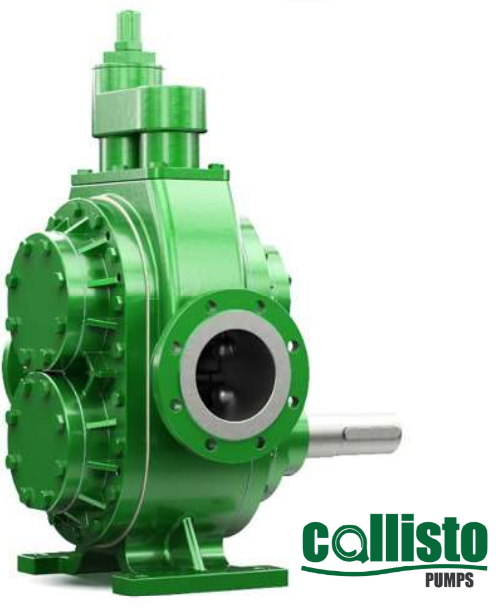
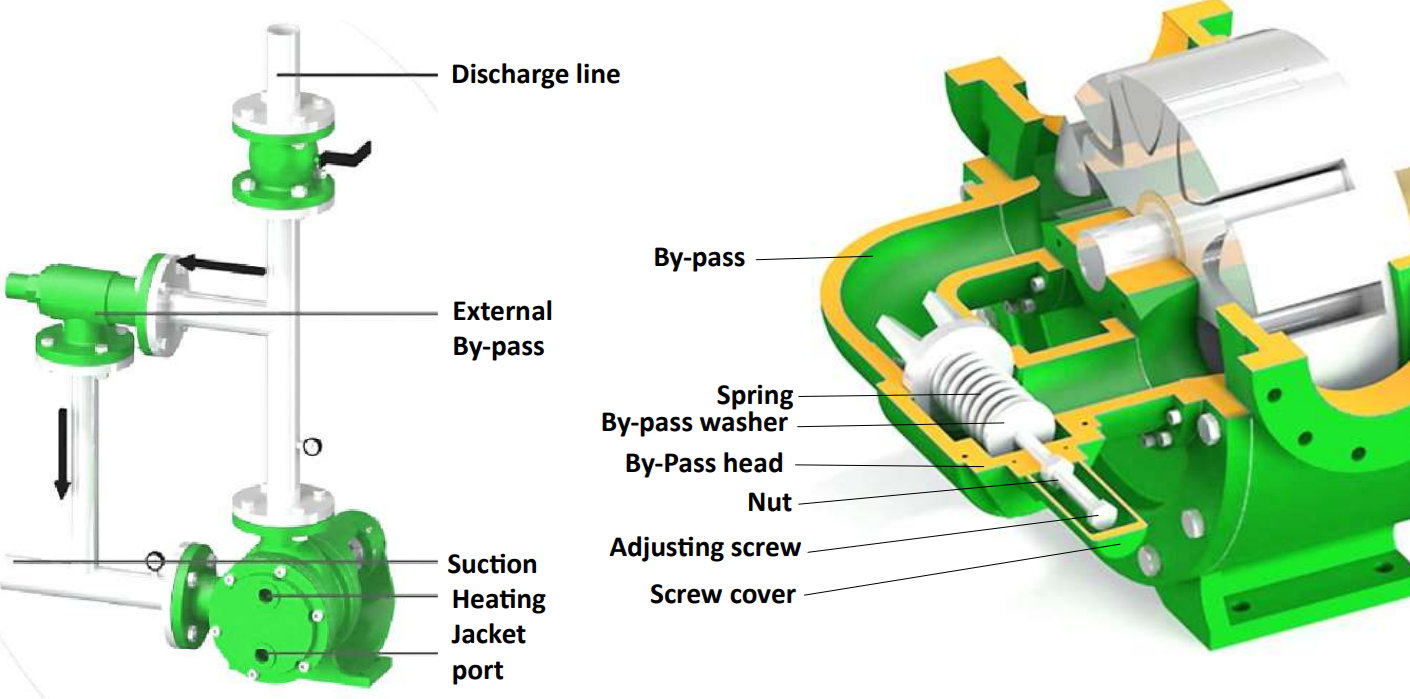
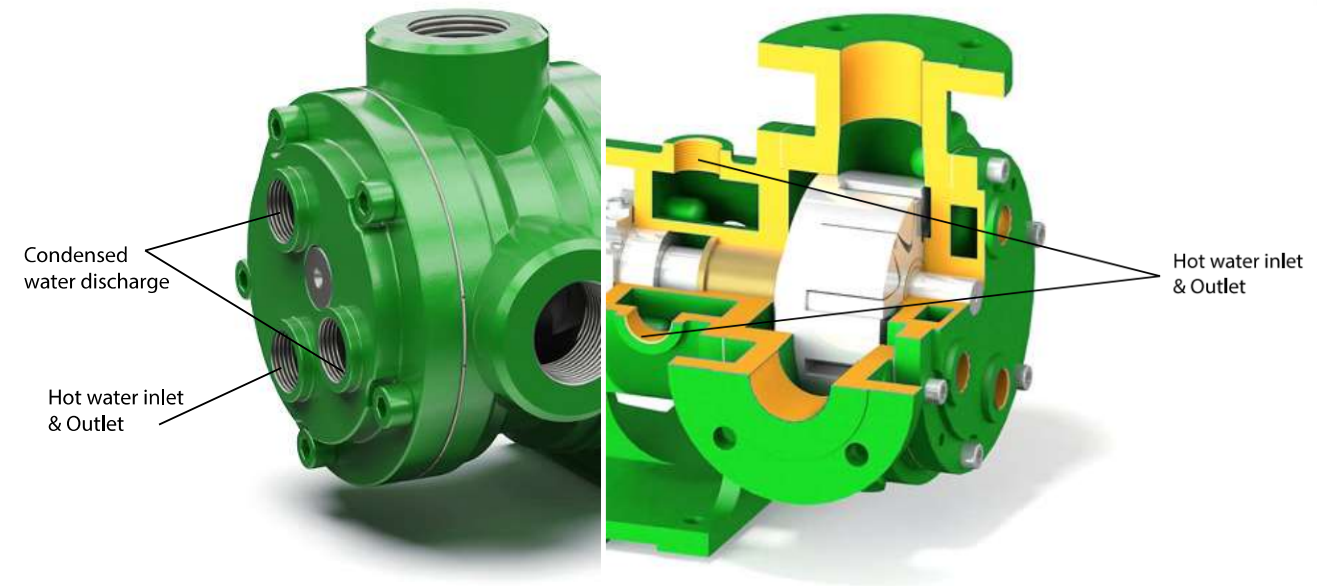
Helical External Gear Pumps
Connection sizes
Capacity range
: 50 – 1500 RPM
Pump body & cover
Cast iron / Spheroidal cast iron/ Cast steel/ Stainless steel AISI 304/ Stainless steel SS316
Sealings
By-Bass / Pressure Relief Valve Operation:
As By- Passes are spring- loaded and adjustable, they can be tweaked in situ to cater for changing system or pump requirements.
Heating Jackets
Maintenance & Troubleshooting
Recommended Operational Checks:
Below is a list of recommended operational checks that will enable operators to extend the life of the pump and avoid
any unnecessary damage.
Regularly check the following:
* Noise, vibration and heat levels.
* Abnormal leakages.
* Flow Rates & Discharges Pressures to ensure that they are within the usual and expected ranges. Having a Flow
meter and Suction & Discharge Pressure Gauges / Sensors are recommended.
* Elastic parts on the Coupling (if present).
* Electrical Current Draws on the motor. If higher than normal this is generally an indication of elevated discharge pressures or blockages within the pump or pipework.
Other Recommendations:
All valves on auxiliary systems should be OPEN.
* If the pump is equipped with a Packed Gland a certain amount of leakage (small drips) is expected. However, if
after prolonged periods of operation this leakage increases then tighten the nuts on the packing press until the
leakage level reverts back to normal. If the nuts are tightened fully then replace the packing gland.
* If the pump is Mechanically Sealed then no leakage should be expected. If leakage is detected then this indicates
that the mechanical seal faces have been damaged and the seal needs replacing. The lifetime of the seal is
application and usage dependent, if you are experiencing undesirable and low seal life please contact our sales or technical department for further assistance.