Menu
Products
- ASME B73.1 Process pump
- ISO 5199 Process pump
- Thermoplastic process pump
- FRP process pump
- Magnetic drive sealless pump
- EN 733 centrifugal pump
- Vertical inline centrifugal pump
- Horizontal multistage centrifugal pump
- Vertical booster pump
- Split case pump
- Self-priming centrifugal pump
- Slurry pump
- Submersible pump
- Vertical submersible cantilever pump (Metal)
- Vertical submersible cantilever pump (Plastic)
- Peristaltic pump
- Air operated diaphragm pump
- Metering/Dosing pump
- Gear pump
- Progressive cavity pump
- Vane pump
- High pressure plunger pump
- Vacuum pump
- Positive displacement Lobe blower
- Hygienic centrifugal pump (FDA)
- Hygienic centrifugal pump (Helical impeller) (FDA)
- Hygienic self-priming centrifugal pump (FDA)
- Hygienic Liquid ring pump (FDA)
- Hygienic Flexible impeller pump (FDA)
- Hygienic Gear pump (FDA)
- Hygienic lobe pump (FDA)
- Hygienic progressive cavity pump (FDA)
Services
Services
Repair, Maintenance and overhauling of rotating equipment (Pump servicing, Blower servicing, Agitator servicing, Fan servicing, Screw Conveyor servicing etc)
Aflowz is a service provider/contractor for pumps, blowers, agitators, fans, screw conveyors etc that offers upgrades, repairs and maintenance on rotating equipment’s in singapore. Because of years of knowledge in rotating equipment’s we know the essential criteria for trouble free operations.
We are able to maximize the performance and lifetime of equipment’s so that our client can count on reliable performance against the lowest cost for their operation.
Onsite service
- Machinery removal, installation, and alignment
- On-site repair: Bearing replacement
- Mechanical seal/ Gland packing replacement
- Equipment maintenance
- Coating
- Shaft laser alignment
- Installation and commissioning
- Pump preventive maintenance
- Blower preventive maintenance
- Agitator preventive maintenance
- Preventive maintenance of static and rotating equipment’s
- Pipe and structural installation
Workshop service
- Pump disassembly
- Casing and Impeller refurbishment
- Shaft straightness inspection
- Shaft fabrication
- Mechanical seal refurbishment
- Seal flush cleaning, refurbishment,
- Ceramic/ Epoxy coating
- NDT inspection
- Dynamic balancing.
- Bearing replacement& Clearance check
- Surface preparation, blasting.
- Coating according to standards
- Assembly
- Hydrostatic testing
- Performance testing
- Mechanical run test
- Installation and commissioning.
modification
We service
- ANSI Centrifugal pumps
- Horizontal split case pumps
- Vertical turbine pumps
- Piston/plunger pumps
- Rotary gear pumps
- Self-priming centrifugal pumps
- Progressive cavity pumps
- Submersible pumps
- Lobe pumps
- Magnetically driven pumps
- High pressure pumps
- Vertical sump pump
- Multistage centrifugal pump
- Liquid ring vacuum pump
- Rotary vacuum pump
- Fire pump / Sprinkler pump
- Marine pump servicing
- Water pump servicing
- Gear box
- Centrifugal fan
- Agitators
- Screw conveyors
- Centrifugal blowers
- Lobe blowers
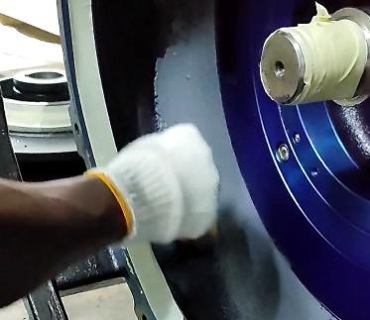
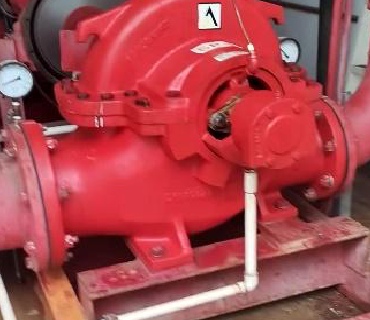
(1) Pump removal at site
We provide 24×7 site service.
(2) Casing and Impeller refurbishment
Use of cold bonding method to mate two materials without any application of heat. Conventional welding process uses high temperature generated by electric arc and gases to fuse two metals. Where else in case of cold bonding two metals can be fused by using adhesives without the use of any heat
(3) Shaft straightness inspection
Shaft runout, Shaft deflection, and shaft whip are issues that occur in industrial shafts. It is essential to check the shaft periodically by which we can prevent severe catastrophic equipment failures in the future.
(4) Shaft fabrication
Shaft of any material grades can be fabricated identical to the existing shaft or client requirement. Damaged shafts also can be refurbished using cold welding techniques.
(5) Mechanical seal refurbishment
Disassembling of the seal and cleaning with ultraclean machine. Surface blasted and polish to get the desired surface finish. Measure the tolerance. Check for nicks, scratches for lapping. Flatness is checked with an optical flat machine. Assembly of mechanical seal
(6) Mechanical seal flushing servicing, modification, installation
To maintain proper lubrication, pressure, temperature, solid management, mechanical seal must be installed with a suitable flushing plan as per the requirement. All the flushing accessories must be periodically maintained to improve the life of a mechanical seal.
(7) Ceramic/ Epoxy coating
Composite Coating can be applied inorder to rebuild damaged casing, impellers, shaft etc. To protect the equipment from corrosion and erosionvarious types of composites like ceramic, epoxy can be applied.
(8) NDT inspection
Liquid Penetrant and Magnetic particle are Nondestructive testing (NDT) for detecting surface cracks or other abnormalities in the material. Magnetic particles are mostly used for castings and Liquid penetrant is for fabrication welds. Radiography and ultrasound inspection are used to detect cracks or flaws below the surface. The intention of these inspections is to detect flaws in the material that could indicate the possibility of a reduction in life.
(9) Dynamic balancing
We offer Dynamic balancing services to correct the most common cause of premature failure in rotating machinery. Unbalance is caused by the uneven distribution of mass around the axis of rotation. If you repair a machine, replace bearing, or perform other service and still experience noise and vibration, you are most likely experiencing unbalance (or imbalance)
(10) Bearing replacement and clearance check
For a proper operation of bearing, bearing clearance is very important. Hence while installing the bearing, it is essential to determine the bearing clearance between the bearing and the contour of the bearing housing. If the clearance between the bearing and the housing contour exceeds the clearance limits, correct shims must be placed to compensate the lost clearance
(11) Surface preparation, Blasting
Blasting can be done according to ISO 8501
(12) Coating according to standards
External and internal coating can be applied according to ISO 19244
(13) Assembly
All the parts will be assembled according to the procedure following all the critical dimensions and clearances.
(14) Hydrostatic testing
All the pumps can be hydrotested to 1.5 times of design pressure.
(15) Performance testing
Pumps can be performance tested according to ISO 99006:2012 (Rotodynamic pumps – Hydraulic performance acceptance tests – Grade 1,2 and 3
(16) Mechanical run test
Mechanical run test can be performed to measure the parameters like Bearing temperature, Fluid temperature and pressure, Cooling water inlet and outlet pressure and temperature, Bearing housing vibration, Shaft vibration, Shaft speed, Power consumption, Mechanical seal leakage rate.
(17) Installation and commissioning
The long-term performance and running cost of a pump can be significantly affected by how well it’s been installed. Our installation and commission services can ensure that the pumps are working properly and according to process needs. We ensure laser shaft alignment, Correct pump start-up, On-site performance verification, Clarification of the actual duty, Measuring noise level, vibration and power consumption.